ここでは再び”おおらかな気持ち“で近似式を使って研磨工程をシミュレーションすることにします。この解説では、全体の加工研磨を研磨速度の関数として表示し、全加工時間を研磨速度で微分し、全加工時間の導関数を求め、導関数が0になる最速の研磨時間を求めます。この際、図1-4で示されている、加工変質層と研磨時間の関係の関数の形がどのような形になっているかが重要になってきて、あまり”おおらかな気持ち“にもなれそうにないようにも思われます。
この解説のモデルでは、適切な研磨条件を考察するときに知らないといけないことは研磨速度と加工変質層の厚みの関係です。実際の実験では、αnanの値を求めることはできると思います。実験結果をもとに研磨速度と加工変質層の厚みの関係をどうやって調べるのかは連載の後の部分で考察します。実験結果をエクセルなどのPCソフトを使って整理する場合、適切な関数の形で実験結果をフィッティングすることは可能だと思います。また、実際に最適研磨条件を探す場合は、研磨速度と加工変質層の厚みの関係は関数で示す必要もなく、入力された多量の実験数値データーから、研磨速度から加工変質層の厚みを直接読みとることもできます。また逆に、加工変質層の厚みから実験データーを使って、研磨速度を示すことは可能です。PCソフトを使って最速解を数値計算で求める場合は関数の形にこだわる必要はありません。
また、当然ですが、図1-4で示されている研磨速度と加工変質層の厚みの関係は、研磨装置や、研磨シート、研磨剤の違いなどの実験条件によっても異なると考えられます。また、砥粒の粒径を変えて研磨速度を変える場合、研磨装置のターンテーブルの回転速度を変えて研磨速度を変える場合、ウエハに加える圧力を変えて研磨速度を変える場合、など、研磨速度と加工変質層の厚みとの関係は、それぞれの異なる曲線上にプロットされると思います。それぞれ、実際の加工作業時の条件で、研磨速度と加工変質層の厚みとの関係を求めます。これらは現象論的な整理です。
1-4. 2段研磨のモデル
最初に加工研磨が2段のみの場合、2段モデルで研磨速度、研磨時間がどうなるのかを考えます。
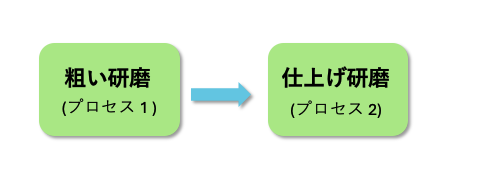
図1-5で示される2段研磨を仕上げる工程を考察します。最初に前節で示した (1-2)式を用いた場合を考察します。簡単に指定するために (1-2)式を(A)式と呼ぶことにします。ウエハの表面には最初、表面の凹凸、加工変質層が存在していて、研磨により削り取らないといけない目標とする加工変質層厚みをSとします。1段目の研磨で削り取る厚みをL1とすると、S=L1です。1段目研磨の研磨速度をv1, 1段目研磨の研磨時間をt1とします。そうすると1段目の研磨では
S =L1 = v1 t1
この関係から、1段目の研磨の研磨時間と研磨速度が示されます。また、この1段目の研磨により以下の厚みの加工変質層P1が新たに導入されています。
P1 = X1(v1) = a1v1,
2段目の研磨で削りとらなければならない厚みは以下のように表現できます。
L2 = α1P1 = α1X1(v1) =α1a1v1
次に2段目の仕上げ研磨でどの程度の厚みの加工変質層P2を達成目標とするかを設定します。P2は最終の仕上げの完成度のようなものです。最終仕上げ目標をFと示すこととします。Fは仕上げ研磨で残留する薄い加工変質層の厚みです。a2はあらかじめ実験的に求めていているパラメタです。a2は既知なので、Fを設定すると2段目の研磨での研磨速度は一意的に決まります。仕上げ研磨の後、それ以後には研磨を行わないので、仕上げの研磨の場合には安全係数α2を考慮していません。
v2 =Y2(F)= F/a2
そうすると、2段目の研磨時間は1段目の研磨速度v1の関数で示すことができます。
t2 = L2/v2 = α1X1(v1) / Y2(F) = α1a1v1 / v2 = [ (α1 a1 a2)/ F ] v1
2段研磨の全研磨時間Tは 以下のように示されます。
T = t1 + t2 = S/v1 + α1X1(v1) / v2 (1-4)
= S/v1 + [ (α1 a1 a2)/ F ] v1 (1-5)
Tはv1の関数として示されています。
Tを最小とする1段目研磨の研磨速度v1と、この時の研磨時間Tが求めるべき値です。
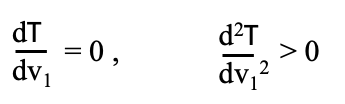
の条件より、それぞれの研磨速度、研磨時間は
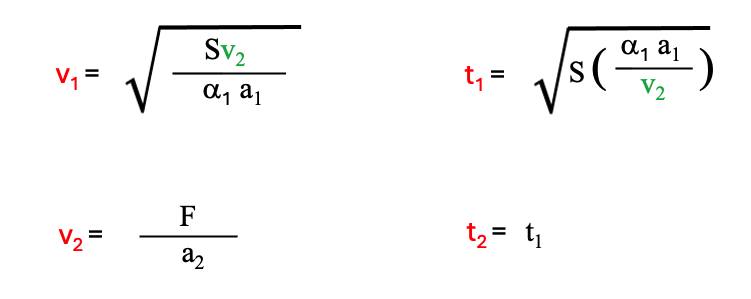
と求めることができます。結果を見ると、最速研磨条件ではt1 =t2 の状態になっています。また、各研磨プロセスの研磨速度も固定されます。

(1-6)
と一意的に解が出てきます。
a1,a2が既知で、1段目の研磨で削り落とさないといけない厚みSと、仕上げの際の仕上がり状態Fが設定されると、2段研磨の各研磨速度、各研磨時間、最速の全研磨時間は一意的に決まります。実際の研磨作業では、それぞれの研磨の後に、ウエハの洗浄時間WTが加わります。1段目の洗浄時間と、2段目の洗浄時間を同じにしておきます。洗浄時間を含めた2段の研磨プロセスの最速時間は以下のようになります。
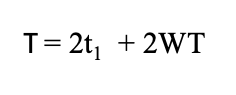
(1-7)
わりと見通しの良い結果に整いました。これらの結果より、2段研磨では、最適な1段目と2段目の研磨速度の組み合わせがあることがわかります。そしてこのモデルだとそれぞれの研磨工程の研磨速度は、研磨速度とそれに依存する加工変質層の厚みに依存しています。それはそういうモデルで考察しているためです。
1-5. まとめ
研削・研磨プロセスの高速化を考察するために、研磨の各工程を統合して考察しようとしています。そのために、研磨の素過程の現象論的なモデルを示し、2段研磨プロセスでの適切な組み合わせ解を求めました。2つの研磨工程を統合した際に、それぞれの工程に対して、ふさわしい研磨速度、研磨時間の組み合わせが一意的に存在していることがわかります。次回では、この2段研磨の最適解について詳しく考察します。また、他の関数(1-3a)式などを用いた場合について考察します。さらに次回以降、研磨の段数を増やして多段工程での最適の研磨工程についての考察を進めます。
この連載で述べていることは、実際に行われている研磨作業を、ある程度整理して表現しています。加工研磨の研究者は最良研磨のレシピを実験的に調べることを行なっていますが、その作業は、αnXn(vn)の値を経験と知識に基づいて実験から見積もっている作業だと、このモデルでは表現されています。