1-1. はじめに
SiCは非常に硬い物質として知られ、容易に手に入る物質としては、ダイアモンドに次ぐ硬さだと認識されていています。このように硬い4H-SiC単結晶を切断し、ウエハの形状に成形し、表面を研磨し、最終的にCMP(化学機械研磨)を行い、ウエハ表面にエピ層成長可能な平滑な状態まで成形するのには多大な労力と時間を必要としています。かつては1枚のウエハの加工に全工程で50時間以上の長い時間を必要としていました。このことが4H-SiCウエハが高価であることの原因の一つでした。そして現在もそれなりに高価です。
SiCウエハの大口径化が進行すると、4H-SiC単結晶の切断・研削・研磨などの加工プロセスでは、従来のウエハ加工装置の改造や、作業方法の改良だけでは、十分ではなくなりました。この15年以上の間、SiCウエハ加工用の新しい装置の開発が進みました。新しい装置の調整と性能の見極めなどが、加工研磨研究者の主な関心事として注目されてきました。そして、個々のプロセス、個々の装置での高速化、大口径化が推進され、加工時間の短縮や、高品質のウエハの成形技術の開発が進行ました。また、今後、SiCウエハのさらなる大口径化が進むことが予測され、さらなる加工研磨技術の進化が期待されています。
SiCウエハ加工技術は、このような高速化、大口径化への対応とともに、一方で高精度化も求められて来ました。図1-1はウエハーの潜傷の例を示しています。これは2010年代前半の3インチウエハの状態を示しています。図1-1(a)はエピ層成長直前のウエハの表面状態です。CMP(化学機械研磨)により傷の無い鏡面仕上げが達成されています。図1-1(b)は、同じウエハのエピ層成長後の状態です。エピ層成長後にスクラッチのような表面凹凸が現れています。エピ層成長後に現れるスクラッチ状の表面荒れを潜傷などと呼んでいます。
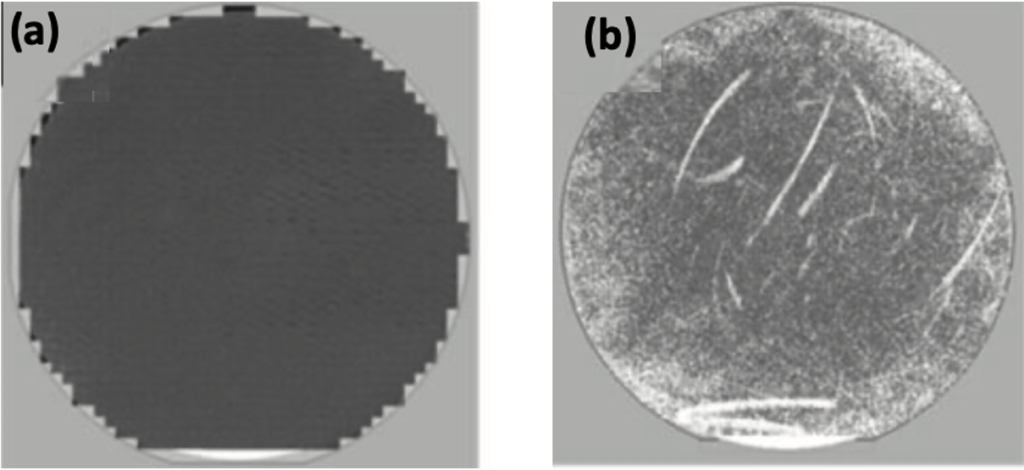
図1-1(a)ではCMPによって鏡面状態になっています。しかしながら、実際には表面より少しだけ深いところに、研磨作業によって導入された転位や積層欠陥などが局所的に高い密度で残留していることがあります。このウエハにエピ層成長を行った結果を図1-1(b)に示します。エピ層成長を行う直前に高温で一度ウエハ表面のH2クリーニングを行います。この時に、研磨によって導入された表面近傍の格子欠陥の局所的高密度部分はエッチングされ、それらの格子欠陥は取り除かれますが、ウエハ表面に凹部分が形成されます。この状態でエピ層成長を行うと、その近辺で巨大ステップバンチングが発生します。そして、エピ層成長に伴い巨大ステップバンチング領域の面積が拡大していきます。この現象については放射光トポグラフ法の応用(10)で詳細を紹介しています。興味がある方はぜひご覧ください。これが発生すると、エピウエハの歩留まりが低下します。
潜傷の問題は、SiCウエハの研磨に高い精度の技術が必要なことを示しています。高い精度の技術の一つは、不均質に局所的に表面から少し深い部分に侵入する格子欠陥を抑える研磨技術です。残念ながらその技術そのものについての言及はこの連載の文章にはありません。実際の研磨作業では、粗い研磨作業から順番に、より繊細な研磨作業へ移って行きます。繊細な研磨作業の際に、余分に厚く研磨作業を行って、深いところに侵入された格子欠陥を取り除く作業を行っています。これらの実際の作業をモデル化し、研磨作業を整理して記述してみたいと思います。
近年の加工研磨に関する技術開発は、個々の装置、個々のプロセスの改良によって達成されてきました。個々の加工研磨装置の開発や、個々の加工研磨技術の改良は、加工研磨技術の研究者間では注目を集め話題になります。そして個々の作業工程での、個々の装置や利用方法の改善により、研磨の、高速化、大口径化を推進して来ました。
そして、その次に考える事は、それらの高速化、大口径化、高精度化した装置をどう組み合わせて、どう利用するかという事です。この連載の文章では、各工程を統合化し繋ぎ合わせて加工研磨工程の全体を考察すると、個々の加工工程で加工速度や加工時間について適切な条件の組み合わせがあることを考察したいと思います。加工研磨作業を、統合化、モデル化して、問題を整理することは、加工研磨工程について、それまでには無い新しい視点での考察になるかもしれません。
筆者は、加工研磨の評価作業に関与した経験はありますが、SiCウエハの加工研磨の専門家ではありません。この連載の文章の研磨のモデルは良くない! より良いモデルを知っているよ!という方がいらっしゃれば、良いモデルを提示していただければと思います。この文章が、SiCウエハの高速、高精度、大口径化、質の良い加工研磨のための議論のさらなる活性化につながればと思います。
1-2. 研磨の素過程

図1-2は、考察するn番目の研磨工程とその前後の工程について示しています。n-1番目の粗い研磨では、粒径の大きな砥粒を用いて研磨します。粒径の大きな砥粒を用いる理由は、表面凹凸や加工変質層をなるべく速く削り落とすためです。n-1番目の粗い研磨を行なったのち、ウエハの表面を充分に洗浄し、n番目の研磨を行ないます。n番目の研磨では、その前の研磨で導入された表面の凹凸や表面直下の加工変質層を削り落とす研磨を行います。このとき、n番目の研磨では、n-1番目の研磨で用いられた砥粒よりも細かい砥粒を用いて研磨します。そして、その後、充分な洗浄を行い、次にn+1番目の研磨を行います。
このように次第に粒径の小さな砥粒を使って、表面の凹凸を小さくしていき、なおかつ表面直下の加工変質層もなるべく薄くしていきます。それぞれの研磨工程では、ダイアモンド砥粒などを金属や樹脂などに埋め込んだ研磨プレートや研磨シートを利用してウエハ表面を研磨します。
最終的にはCMP(化学機械研磨)で仕上げ、表面の凹凸と、表面直下の加工変質層をなるべく薄くすることを行います。この解説で考察するモデルでは、切断、研磨、化学機械研磨も同じモデルで考察します。
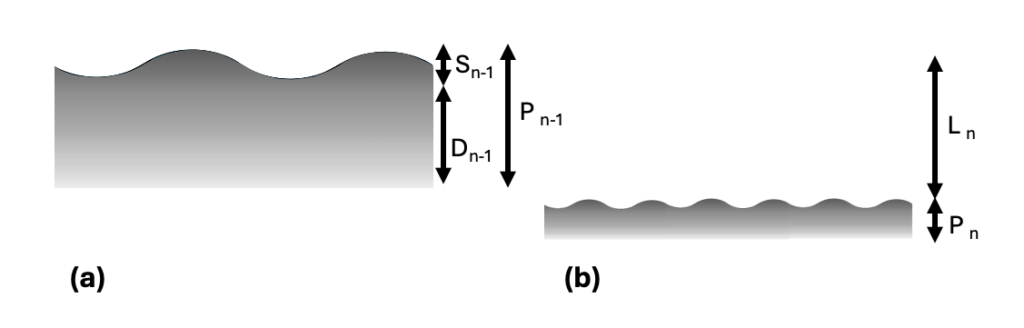
図1-3 (a)は 図1-2のAの時点での表面近傍のウエハ断面の模式図です。表面には大きな凹凸が形成されています。Sn-1はn-1番目の研磨により表面に形成された表面凹凸の深さを示しています。Dn-1はn-1番目の研磨の後に表面直下に形成された格子欠陥が多量に存在する層の厚さを示しています。一般的にDn-1は加工変質層と定義されますが、ここでは話を簡単にするために、Pn-1=Dn-1+Sn-1をn-1番目の研磨で導入された加工変質層の厚みと定義します。
図1-3 (b) は図1-2のBの時点での表面近傍のウエハ断面のモデル図です。n-1の研磨で導入された加工変質層を取り除くため、Lnの深さをn番目の研磨で削り落としました。n番目の研磨では、n-1番目の研磨で利用した砥粒よりも粒径が小さな砥粒を用いて研磨します。この時、Pn-1< Lnになるように研磨します。そしてこの研磨によってPnで示されている小さな凹凸、薄い加工変質層を新たに作り出しています。